Rapid Tow Shearing Technology
Produce lighter, more sustainable and cost-effective structures with the Rapid Tow Shearing (RTS) process for composites.
Talk to an expertRobust
Defect-free steering regardless of the tape width and thickness.
High-rate
Fully automated production capable of high deposition rates.
Material agnostic
Compatible with off-the-shelf materials.
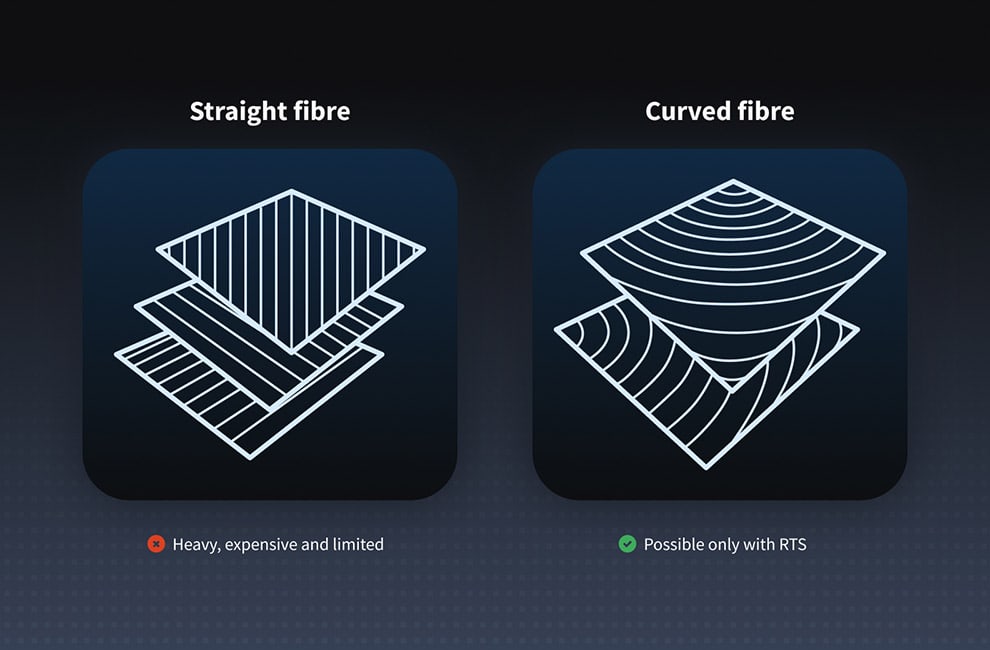
Disruptive principle
Composite layers consist of millions of aligned fibres leading to exceptional stiffness and strength only in one direction.
So far designs have been restricted to straight fibre layers due to manufacturing limitations.
The result is heavy and expensive structures using more material than needed.
A world first
Our patented process enables defect-free steering of composite tapes along curved paths for the first time.
By shearing tapes instead of bending, we overcome showstoppers of current technologies.
RTS sets new rules changing the way we design and produce composites.
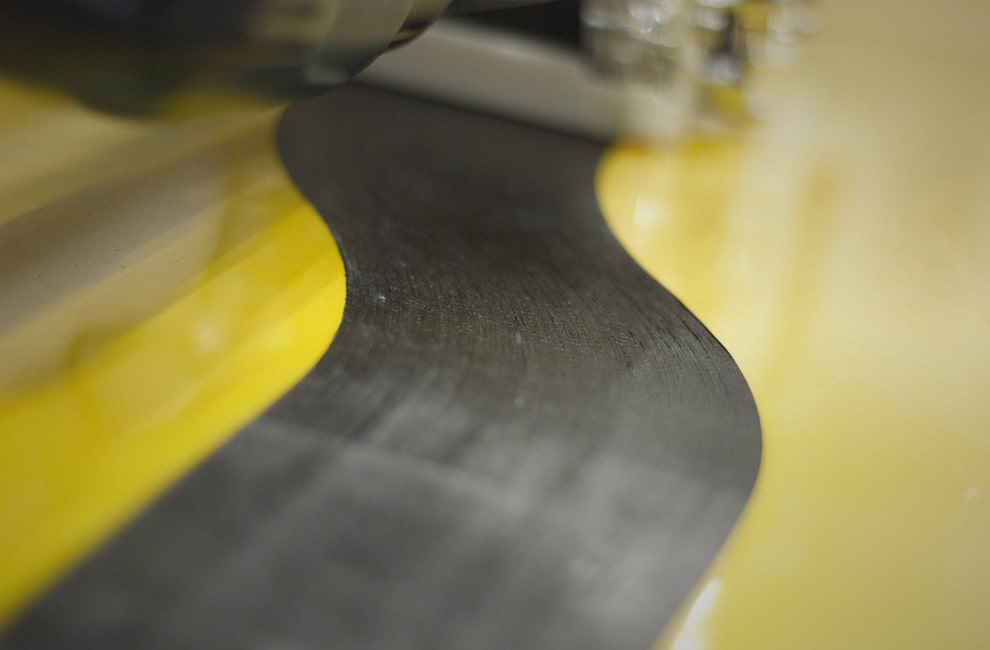

Unmatched performance
Fibre steering allows the efficient placement of tapes following load paths, delivering highly-optimised structures with dramatic weight savings and lower use of raw material.
Fundamentally sustainable.
Contact us today to discuss how our next-generation solutions can transform your product.
Talk to an expert